Actros versus Actros!
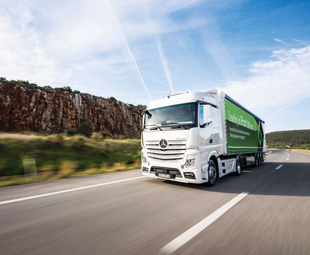
Mercedes-Benz recently organised an utterly fascinating test in Portugal, where it pitted the Actros against itself! The results of this test were astounding. Then the company invited the International Truck of the Year jury to Portugal to explain how these “miracle” results could have been achieved. CHARLEEN CLARKE was there …
Imagine a tennis match in which Milos Raonic is playing Milos Raonic.
Does this sound a bit daft? Maybe, but work with me here … use your imagination. The one player is Raonic in 2011 – when he earned the paltry sum of $674 966 (R8,9 million) in prize money. The other is Raonic in 2016 (when his prize money sky-rocketed to $5 588 492 … or about R73,9 million).
Along the way, he’s become a whole lot better. The current Raonic should thump the earlier Raonic. As they say in the (South African) classics: do you catch my drift?
Now the same should really apply to trucks, and, in most cases, it does. The latest models are, indeed, much better than previous derivatives. However, Mercedes-Benz recently decided to put this to the test.
Testing times
This was done very scientifically: the truck manufacturer engaged the services of six transport journalists who tested two Actros 1845 vehicles – a first-generation Actros, which was in production until 2015, and a current Actros 1845 with what the company is calling “the second-generation powertrain”.
The journalists drove the trucks on a hilly route between Tavira and Lagos on the A22 motorway in Portugal’s Algarve. The total distance covered was a whopping 4 800 km.
The A22 represents the perfect test route; there’s little traffic out of peak tourist season and the gradients are challenging (although they do pale into insignificance compared to Van Reenen’s Pass).
Naturally, the test was extremely scientific; in typical German fashion, they adopted a methodical and highly accurate approach to measurement. I could go into enormous detail … but then this article would fill this entire issue of FOCUS. So, you’re just going to have to trust me on this.
Incredible results
The results of the test were quite astounding. Back in 2016 at the IAA, Mercedes-Benz promised that the new Actros with its second-generation powertrain would deliver fuel savings of up to six percent (versus its predecessor).
However, when Predictive Powertrain Control (PPC) was activated on both test vehicles and set to eco mode, the journalists achieved a staggering 10,6-percent saving! How on earth could they have managed this?
International Truck of the Year jury enters the fray
In order to establish the answer to this question, the International Truck of the Year jury travelled to Portugal. We wanted to find out how it was possible to slash your fuel bill by almost 11 percent! And so we did…
Interestingly, there isn’t one magic wand that gets waved. Instead, Mercedes-Benz has done lots of things. Each of these helps to lower fuel consumption – sometimes by as little as a fraction of a percent. The drive axle on the latest Actros, for instance, is equipped with a needs-based variable oil supply, and it reduces consumption by 0,5 percent, but, when you add all those “things” together, that’s when you get the abracadabra.
So exactly what are all these “things”?
Optimised engine
Clearly, the engine is rather important – and the very latest OM 471 ticks all the boxes. It offers a three-percent fuel saving (versus its predecessor). The engineers achieved this by enhancing vehicle dynamics at the lower end of the engine speed range most of all – and thus capitalising on a further reduction in consumption at the same time.
One of the methods employed by the engineers, in their quest to lower fuel consumption, involved fiddling with the injection system. The current Actros boasts the latest-generation X-Pulse injection system – the unique common-rail system with pressure booster in the injector and unrestricted flexibility for modelling the injection process. Maximum rail pressure has been increased from 900 to 1 160 bar, resulting in a maximum injection pressure of 2 700 bar now (versus 2 100 bar in the Actros models of old).
The biggest news, when it comes to engines, is the significantly increased torque at the bottom end of the engine speed range. This means that peak torque is available from just 800 r/min with the latest-generation OM 471 (versus 1 000 r/min for its predecessor). Naturally, this makes lower revs accessible. A new asymmetric turbocharger is partly responsible for the swift and substantial increase in power delivery at low rev speeds.
The aforementioned engineers also turned their attention to the asymmetric turbocharger, which has been one of the special features of the OM 471 engine from the very start. To ensure fast build-up of the boost pressure combined with a correspondingly quick surge in output and torque, the exhaust gases from cylinders four to six are forwarded directly into the turbine.
A defined quantity of the exhaust gases from cylinders one to three, on the other hand, is diverted for exhaust gas recirculation. This serves to reduce the NOx emissions. This solution has been retained in principle, but greatly improved upon when it comes to the finest details.
The previous EGR flap in the EGR path, for instance, has now given way to an EGR flap repositioned much further forwards in the exhaust manifold, which is some distance before the exhaust gas enters the turbocharger. Thanks to the flap’s new position, both the EGR rate and the exhaust gas flow to the turbocharger can be controlled in accordance with the engine’s operating characteristics.
Asymmetric injection is another new feature. In normal driving operation, the injectors for all six cylinders of the OM 471 are supplied with the same quantity of fuel. If regeneration of the diesel particulate filter is required at low loads, a high EGR rate of up to around 50 percent is set in order to raise the exhaust gas temperature.
Keeping it simple
The engineers also came up with another clever idea: they reduced the number of components and parts in the engine. This doesn’t impact on fuel consumption, but it does play an important role when it comes to another factor: uptime. The thinking behind this move is that anything that’s not fitted in the first place can’t cause a malfunction. This is such a simple concept, but actually so clever!
New low-friction engine oils
Mercedes-Benz is now making use of high-temperature, high-shear (HTHS) engine oils. These are fully synthetic multi-grade low-friction oils in various viscosity classes between 0W-30 and 5W-40. These low-friction oils reduce friction losses in the engine at operating temperature, resulting in lower fuel consumption.
More advanced transmissions
The Mercedes PowerShift 3 12-speed transmission has also received some attention. The goal, naturally, is to reduce friction losses. As such, the engineers turned their attention to the two constant-mesh gears of the splitter group.
As these are always engaged, efficiency plays a particularly important role here. They optimised the surfaces of the tooth flanks, using a so-called Superfinish production process. They are polished to the point that they’re as smooth as glass! Absolutely no unevenness is discernible – even when you touch them with your bare hands. Friction losses in this specific area were reduced by 50 percent – and the engineers say that they’re now at the limits of what is technically feasible.
PPC now even better
PPC isn’t new; it was launched back in 2012, but, goodness gracious me, it really does a terrific job. We drove the latest Actros over an undulating route from Lisbon to the delightful seaside village of Peniche, and PPC is honestly just a dream, because it does all the thinking for the driver (the truck rolls, accelerates and changes gear in anticipatory mode, depending on the topography).
Now, driving with PPC is even more efficient. The shift points of the anticipatory cruise control have been optimised – and the Ecoroll phases are longer than before. Practically speaking, this means that – even before the truck reaches a summit – the vehicle can now roll for longer. It’s a really incredible system that doesn’t just make the life of a driver so much easier – it saves fuel, too.
Alternator saves energy, too
The design engineers also turned their attention to the alternator and to finding new ways of saving energy there. They came up with a brainwave: a new alternator that no longer supplies voltage continuously, instead this can vary between 24 and 30 V (depending on the truck’s requirements).
Aerodynamics gets attention
Aerodynamics obviously also played a prominent role in developing the new generation of trucks from Mercedes-Benz. Because the engineers were so determined to develop a fuel-efficient truck unlike any other, the current Actros spent 2 600 hours in the wind tunnel (that’s unprecedented).
There are many innovations that have resulted. Just one is the new shape for the rear spoiler on the
2,5-metre StreamSpace cab of the Actros.
So, there you have it. These are just some of the ways in which a truck can be optimised (I’ve just scratched the tip of the surface; Mercedes-Benz did lots of other frightfully clever stuff, too). Roll on the days when the very latest trucks arrive here in South Africa!
Published by
Focus on Transport
focusmagsa
