Improving log loading efficiency
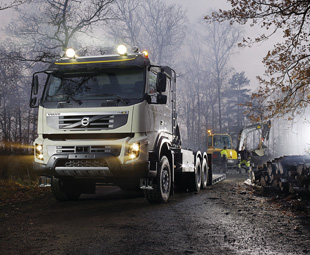
Several modes of transportation are used in the forestry sector worldwide, but truck transportation constitutes an important part of the supply chain. CLAIRE RENCKEN takes a look at how it can be optimised.
Take Ireland for example … in 2007, forests covered ten percent of Ireland’s land area, and this is projected to increase to 17 percent by 2030. This volume increase will have a direct correlation and impact on the logistics involved in the wood supply chain.
According to the European Conference of Ministers of Transport, freight transport was set to grow from 50 to 60 percent by 2015, from the 2001 values. So, road transportation is, and will remain, the most important mode of timber transport in Ireland; forming a substantial part of the industry’s raw material cost and having a major influence on the sector’s overall economic performance and competitiveness.
The transport of wood from the forests to the industries is carried out by trucks of different makes and models. The trucks are usually differentiated by the number of axles, axle spacing, tare weight and the engine position in relation to the front axle.
All European countries impose haulage regulations related to the restriction on dimensions and weight of the trucks. The weight restriction is more complex, due to the relationship between number of axles and the distance between them, and this affects loading of the vehicle in terms of gross vehicle weight (GVW).
Ireland sets a maximum of 44 000 kg for trucks with six axles (soon to be increased to 46 000 kg), and
42 000 kg for five-axle trucks (proposed to be reduced to 40 000 kg). The truck’s weight is monitored at weighbridges and overloaded trucks incur penalties, normally of a financial nature, or in the form of a ban on transporting timber for a specified period of time.
As everyone in the trucking industry knows, overweight trucks can cause problems such as deterioration of roads, short vehicle life, difficulty in manoeuvring vehicles and safety issues. Of course, fuel consumption also increases with the weight of the vehicle.
The challenge facing truck operators is to place enough material on a truck (and trailer) of fixed dimensions, in an efficient manner. Obviously, carrying less than the legal maximum weight is not economically viable. In the case of wood biomass (chips and bundles), low density can decrease the productivity in transport with loads reaching the maximum legal dimensions of the truck and/or trailer before meeting the legal maximum weight.
In the case of logs, the situation is different; the material has a higher bulk density in comparison to bundles and woodchips. Maximising the load involves attempting to reach the full load volume capacity without exceeding the legal maximum weight.
Another way to potentially increase efficiency in transportation is to reduce the variability of the GVW. Less variable GVW yields higher net payloads.
Factors such as wood moisture content, dry matter, solid and bulk density and truck payload constraints all need to be evaluated in order to deliver the material cheaply and efficiently.
Truck hauliers need a way to determine, in-forest, the optimum volume and payload weight of wood to be transported, by knowing the wood moisture content and using the height of the stanchions of the trailer as a reference point to improve the overall log loading efficiency.
Weighing in-forest through an on-board system generally reduces the variability of GVW, increases the payload (by minimising the light payloads) and reduces the possibilities of financial penalties due to overweight trucks. However, implementing on-board weighing systems constitutes initial capital investment to install such a system, together with the increase in managerial duties in order to effectively use the information it provides to the benefit of the haulage company.
Caterpillar keeps drivers alert and alive
Operator fatigue and distraction can result in deadly accidents when using heavy forestry equipment. Caterpillar has launched a monitoring service to help manage operator fatigue.
Property damage, increased fuel burn and tyre abuse have also all been tied to fatigued or distracted operators. Caterpillar has launched an equipment operator monitoring service to help manage the human factor in the operation.
In-cab and wearable safety technologies give customers visibility to both machine and operator information. Caterpillar’s 24-hour monitoring centre contains analysts who correlate data, about the health and productivity of operators and equipment, to reveal the magnitude of conditions such as fatigue and distraction and their impact on operations.
Various technologies were used to develop the monitoring system. The Driver Safety System (DSS), developed by Seeing Machines (an alliance partner of Caterpillar) includes an in-cab camera and alert system to notify the operator the moment a fatigue or distraction event occurs.
These events are tracked by analysts who also capture operator sleep quantity and quality information provided through the wrist-worn Cat Smartband, an actigraphy solution powered by Fatigue Science.
The enhanced visibility to risks extends beyond frontline employees to expose improvement opportunities throughout the organisation including: education and training, shift scheduling, leadership coaching and other cultural elements.
Published by
Focus on Transport
focusmagsa
