Necessity: the mother of invention
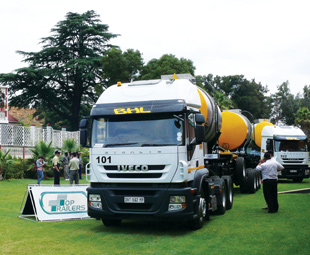
The concept of a multi-purpose tridem semi-trailer has been tried before, and not with much success. But this time round, the revolutionary BuckSta could be the solution African operators have been dreaming of, writes UDO RYPSTRA
Necessity is the mother of invention, Plato once said. The expression still holds today and this includes the road transport industry, which faces ongoing challenges to contain regular increases in the cost of vehicles, fuel and labour, to name just a few.
In this respect, proper load optimisation is the name of the game and can be a constant headache for operators having to deal with empty return legs. Buks van Rensburg, a South African transport operator who sold his South African transport business, Coma Transport, to black empowerment group, Africa Resources, in 2003, has been sitting with that headache since 2004 when he opened a new transport business in Zambia. His new company, BHL Zambia, operates on the Copperbelt hauling copper concentrates in side-tippers from mines near Kolwesi to a copper mill 240 km away, and returning empty for the next load.
At the same time, he has been operating tankers to bring in sulphuric acid from opposite directions, and again, seeing them return empty for the next load.
As every seasoned operator knows, this is a far cry from load optimisation with all the empty legs obviously having to be charged in – the customer pays.
In a similar fashion, Van Rensburg has been operating flat deck trailers carrying bagged grain from outlying farms to flour mills and tankers bringing in cooking oil. Again returning empty. And, the customers pay for all the empty legs as well.
He soon realised that there had to be a solution to the empty leg problem.
Van Rensburg is no stranger to entrepreneurship, innovation and invention and it showed – plus a lot of guts – during his years as owner of Coma Transport and through his transport experience prior to that. One of the many things he learned is that if you want to keep rates low and, therefore, customers happy, plus make a decent profit at the same time, you need to reduce empty legs to the minimum.
Like many entrepreneurs, he learned this by working his way up the ranks, having started his transport career as a driver for Presto, followed by a two-year stint with Rauties as transport manager and a further period working for Road Corp. In between, he also studied law and engineering. In the mid-90s he took the plunge to become his own boss by registering a shell company in 1992 – Coma Transport, in Boksburg. He didn’t have a single truck, but a sound understanding of budgeting and costing which helped him win a tender put out by Montigny Investments in Swaziland. The tender was for the transport of timber from Swaziland to the Mondi Mills at Richards Bay. In fact, Van Rensburg met his obligations by sub-contracting the work to H Muller Transport.
During those early years hauling timber, Van Rensburg learned the art of load optimisation by diversifying into other fields, including sugar from the Lowveld and Swaziland with backloads of cement, cooking oil and general foods. He watched those backloads very carefully, achieving 99% full loads. By doing so, he used additional subcontractors, but also started buying his own Iveco trucks in 1999 and began comparing his own costs with other makes operated by his subcontractors.
By the time he sold, the fleet consisted of nearly 50 truck-tractors – most of them heavy duty Iveco EuroTrakkers, which have proven to be extremely reliable trucks and the Iveco brand once again forms the core of his Zambian based fleet today.
The new business has mushroomed. BHL Zambia now operates 75 truck-tractors, which include a number of MAN trucks. But the problem has been optimising the payloads of all the tipper and tanker they haul, especially in Zambia.
The solution? It’s all about innovation, if not inventiveness. The concept of a big dual purpose semi-trailer is not new – it has been tried overseas (eg logs and wood chips) and was tried in SA about a decade ago with Mepalink trailers that could carry liquids and solids in two separate compartments – the latter on top of the former.
Prototypes were built, but the concept never took off. This time, Van Rensburg came up with the idea of a trailer which could carry a tank for liquids up front on the semi-trailer, a side-tipper in the middle, and another tank aft on the tridem axle. For this, he approached one of South Africa’s most highly respected tipper manufacturers, Top Trailers, with whom he has had a relationship for more than ten years, and also Flexi Manufacturing, just as well known for its top quality liquid (milk, etc) and chemical tankers.
“Top Trailers don’t make tankers; Flexi Manufacturing don’t make tippers. This made for a perfect partnership,” Van Rensburg mused. When it comes to tipper design, brothers Riaan and Louis van den Berg, co-directors of Top Trailers, have made a name for themselves by not only being innovative, but also for producing trailers that are durable and meet the highest international technical and safety standards.
Van Rensburg, however, wanted a durable trailer that could withstand worse conditions than those found in South Africa. A trailer that could handle Africa’s rough terrain, notorious potholes, and which could haul as many commodities as possible.
Spokesmen for both trailer manufacturers said Van Rensburg’s idea was a viable one. The end result, after a great deal of research and development by all three parties, is a “revolutionary” dual purpose trailer called the BuckSta, which has two 8 000-litre tanks placed, as requested, with a side-tipper bin capable of carrying 28-tons of copper concentrate in the middle – all of which can be removed to accommodate other load bodies such as 3m containers.
According to Riaan van den Berg, Top Trailers is receiving an increasing number of orders for its trailers from cross-border customers, built for truly African conditions. The BuckSta trailer chassis design features a trailer of high tensile steel which was reinforced in many ways to absorb Africa’s bad road conditions. Instead of the usual European or local axles, it incorporates Mondo axles with highly tempered beams and suspension, manufactured in China.
“They are distributed by a local company and we chose them because from a maintenance position, the parts are more easily accessed in Africa. Nevertheless, the trailer is fitted with the Wabco ABS system and an automated system to improve proficiencies in respect of the tipper load. Instead of a tarpaulin cover, the hydraulically operated, galvanised top cover cannot be tampered with. While it also protects commodities such as copper concentrate (worth about US$75 000 in this case), it also seals better than a normal tarpaulin.
“The materials used in manufacturing of the galvanised top are also a lot more durable than any other top currently on the market.”
According to the three parties, this trailer is unique in that it is able to haul dry bulk product like chrome in one direction and liquid bulk like molasses in another direction on the return leg in separate stainless steel tanks. In instances where one commodity is a food product and another commodity is a toxic substance, there is no chance of contamination due to the separate containers.
According to Percy van der Merwe, manager: Flexi Manufacturing, they can be used for both hazardous and non-hazardous liquids, providing that proper decontamination procedures are followed. “The stainless steel tank is mounted on standard container locks. This is not only durable and versatile but also adds additional value in the sense that there is an aftermarket for the tankers. Any other container can also be mounted to the trailer should the transport contract change,” he said.
The trailer can therefore be completely customised to the client’s exact application requirements. The design is also extremely flexible regarding transportation of different commodities with a high specific gravity (SG).
According to Van Rensburg, it will provide cost savings of up to 20% in terms of logistics for mining houses, the agricultural and also construction industries, due to the ability to transport different products on the same trip. “I will be able to reduce my rates, not increase them,” he said.
Indirectly, it also provided a cost saving to the end user/public due to the saving on distribution cost of the transported goods. Safety risks on mine sites would improve due to less traffic in the mining area while safety on national and international roads will improve due to better utilisation of transport equipment. “And for operators like me, it will mean a substantial increase in profit margin due to better utilisation of the equipment.”
The first two concept trailers have been completed and will be operating on contract by BHL for First Quantum Minerals Ltd from 15 February 2011 at their Kansanshi mine in Solwezi, Zambia. The trailers will be transporting copper concentrates in one direction and return with sulphuric acid on the return leg.
Meanwhile, both Top Trailers and Flexi Manufacturing have their sights set on increasing their cross-border market penetration with products that are tapered to customer requirements. Incorporated in 2002, Top Trailers is one of the largest truck trailer manufacturers in South Africa and is also known for offering clients excellent after-sales service.
The company also sells used trailers and rents out trailers which are part of their assets. The fact that they also offer their clients 24-hour roadside assistance in case of a breakdown ensures that they offer the best after-sales service in the country.
The management team, which started the company over eight years ago, is still running the company in a totally hands-on fashion. Flexi Manufacturing, which took over the well-known Clover trailer manufacturing plant (for milk tankers) in Heilbron, Orange Free State in 2004, today specialises in the custom design and manufacture of a wide range of stainless steel, mild steel and GRP vehicle load bodies. It has adopted a competence area approach to describing the products and services it provides and has further extended its business to value added engineering services that set it apart from traditional truck bodybuilders.
With the unbundling of Imperial Holding and the creation of EQSTRA holdings in May 2008, Flexi Manufacturing extended its focus to the support and assembly of products for the blue chip businesses aligned with the core focus areas of EQSTRA.
Published by
Focus on Transport
focusmagsa
