To reuse or recycle, that is the question
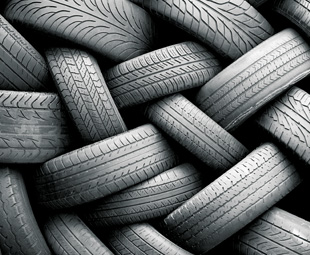
What is being done to counteract the negative effect that used tyres have on the environment? With different entities sharing one goal, there might be hope after all – Deon van der Walt finds out more.
Tyres are, arguably, one of the most crucial components of any motor vehicle. A passenger vehicle’s safety depends on its tyres being in good condition, while tyres can have a direct impact on a commercial vehicle’s productivity.
The mid-nineteenth century was the Genesis for the tyre as we know it today, when Charles Goodyear invented vulcanized rubber, which would later become the rubber used for the earliest tyres created by inventors with similar, yet very different, ideas. Since then, all road transport has become reliant on tyres.
This poses an important question in the framework of “global warming”. What happens to these tyres when they are no longer usable?
Annually, South Africa adds 11 million tyres to already problematic landfills and open areas. Designed to be extremely durable, tyres are notoriously difficult to recycle and take very long periods (up to 50 years) to biodegrade.
Instead of just discarding the bald, worn-out rubber to disintegrate, recycling or reusing will help save the planet – one tyre at a time.
The Recycling and Economic Development Initiative of South Africa (Redisa) plans to clean the country of tyre waste. According to Redisa, there is a growing demand for waste tyres that can be recycled and used to manufacture products made from the rubber, steel and textile derived from the processed tyres.
With 34 operational depots in all nine provinces, Redisa created 1 617 jobs and collected 81 542 t of waste tyres in the period from December 2013 to December 2014.
Director Stacey Davidson says that Redisa is not a recycler, but supports companies that recycle and process waste tyres into saleable products.
“Our support ranges from business plan development, to assisting with environmental impact assessments. We offer regular delivery of waste tyre feedstock to all recycling companies that are registered with Redisa,” says Davidson.
One such operation is the joint venture between the Mathe Group, based in KwaZulu-Natal, and PFE International. These two organisations plan to build a multi-million rand rubber crumb manufacturing facility in Hammersdale.
Mehran Zarrebini, head of PFE International, says that the new facility will be home to the Mathe Group, and is one of only two KwaZulu-Natal companies registered with Redisa.
The Mathe Group, which currently recycles tyres at an 850 m² factory, will significantly increase productivity with the new manufacturing facility. Due to be commissioned in April, it consists of a 2 500 m² factory and a 1 000 m² warehouse, and will feature modern equipment worth R20 million.
Bandag (which has been operational in South Africa for more than 40 years) offers an alternative solution to cut down the ever-increasing number of waste tyres – in the form of retreading.
“Retreading as a discipline is the first step in recycling efforts. With retreading you extend the service life of tyres, thus reducing tyres at landfills. In this way, the legacy scrap pile of tyres can be worked through the government’s recycling efforts, which Bandag fully supports,” says Bandag marketing manager Monal Naik.
Bandag has a strict set of criteria to optimise the retreadability of truck tyre casings. These include: the selection of the correct tyre/casing for the desired application, timeous tyre removal and a proper tyre inflation maintenance programme.
“Modern premium-quality retreads are on par with new tyres and will almost certainly outperform budget tyres. With its multiple ISO certifications, Bandag is making sure that the manufactured product has the highest level of conformity and reliability,” continues Naik.
Bandag offers a guarantee on its products with a further guarantee against faulty workmanship or defective materials used; helping to reduce the impact of waste tyres on the environment, for a sustainable future.
*Deon van der Walt is the South African Guild of Motoring Journalists’ bursar student. He recently spent a month with FOCUS, where he was exposed to the local commercial vehicle industry.
Published by
Focus on Transport
focusmagsa
