Tyre recycling gets the green light
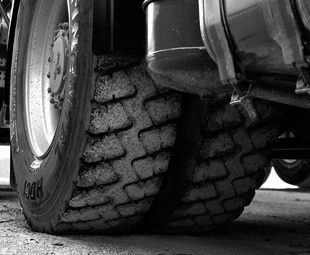
Tyre recycling in South Africa may now get off the ground after a long-winded debacle and a court ruling in May. Is this the final step that will open the way? What does the future hold? FOCUS brings the latest news on this important topic.
In a decisive court case in May the Supreme Court of Appeal dismissed an appeal by the Retail Motor Industry Organisation (RMI) for an interdict preventing the implementation of the Recycling and Economic Development Initiative of SA’s (REDISA’s) waste tyre management plan.
The court set aside every reference to solid tyres in REDISA’s plan but stressed that this “does no violence to the objects of the plan” and that the court left the remainder of the plan in place and consistent with the waste tyre regulations. All other arguments advanced by the RMI were rejected.
Hermann Erdmann, REDISA’s chief executive, says the implementation of its plan, which had been delayed for more than 12 months due to court proceedings, would now be ramped up to deliver against the mandated targets.
Jeff Osborne, RMI CEO, reacted by saying, “The RMI is concerned that, as a result of the outcome of this appeal, it may no longer be possible to have the remaining provisions of the plan reviewed and set aside.
“The RMI’s legal team will consider the implications of the judgment and the options that may still be open to the RMI. In our view the judgment by the Supreme Court of Appeal has clear constitutional implications for the whole of the industry as well as for members of the public, and it may be preferable that the Constitutional Court be permitted to have the final say.”
Tyres are among the largest and most problematic sources of waste due to the large volumes produced and their durability. Erdmann explains the rationale behind the need to recycle tyres in an effective way. “Many industries produce, directly or indirectly, environmental problems that have to be dealt with,” he says. “Mining, for example, directly damages the environment and mines are obliged to make provision for rehabilitation of their operations on closure. An industry like the tyre industry results in large quantities of waste products that are an environmental hazard and somebody has to deal with the problem.
“Tyre collection and recycling is not economically viable without some form of funding to support it,” Erdmann maintains. “To address this, REDISA is putting into practice a ‘polluter pays’ principle similar to mines contributing to a rehabilitation fund: tyre producers (manufacturers and importers) will pay a waste tyre management fee, which is then applied to the collection and recycling of old tyres. Every tyre produced must be disposed of ultimately, and provision for the cost must be built into the manufacturing cost.
“The proposed levy is relatively small taking into account the life cycle and distance a tyre will travel in that time,” he says. “The levy is not a tax; it’s a rehabilitation fee that makes the programme viable.”
REDISA is sponsoring research at local universities, the intention of which is to establish further uses of rubber as a product, in addition to developing environmental ratings. These programmes examine (among other things) ways to extend the useful life of tyres so that the backlog of tyres in need of recycling decreases, resulting in a reduced fee being required.
According to Erdmann, the benefits to the consumer and the economy are:
• The environmental problem is dealt with proactively, rather than reactively, and a proactive approach is always less expensive in the long run;
• Something regarded as waste is transformed into a resource, for example rubber crumb;
• More environmentally friendly and longer-lasting tyres will reduce both the long-term cost to society and save consumers money.
“The programme is leading to a change in attitude,” says Erdmann, “and will create a number of secondary industries that will positively impact the transport, logistics and other industries.”
The South African market manufactures, imports and sells well in excess of 10-milllion tyres (or about 270 000 tonnes) annually. The target is to grow recycling from an initial 30 000 tonnes to over 300 000 tonnes per annum in five years.
To establish a tyre recycling plant can cost as much as R700 million, and the programme has to be attractive enough to draw investors. The plants will be fed from numerous depots to be established around the country.
A system will be created to collect and transport tyres to the depots and plants free of charge. This has already led to more than 300 companies applying to participate.
It is estimated that 10 000 new jobs will be created in various ways which means many more people will benefit, as most of the jobs will be filled by family breadwinners. The programme will create a number of secondary industries in the transport, production, distribution and marketing areas.
A long supply chain starts with transporting old tyres to the depots and then to the plant, creating opportunities for transporters and especially owner-drivers and their crews. The plant itself will require operators and general labourers. Next comes the distribution of the reclaimed materials and by-products; these then will be used in various manufacturing processes, and the end products have to be distributed and marketed.
There are also other benefits. For example, the need to burn tyres to recover some of the materials such as the steel reinforcing will be eliminated. The rubber crumb and powder, and the steel recovered at the plant are all easily processed into usable products.
The recovered materials are valued at R2 000 to R7 000 per tonne as against the valueless tyres submitted to the programme.
Uses are varied: Rubber bricks, being water resistant, are especially suited for damp-proof layers; roof tiles are durable and offer the safety of being fire-resistant; bollards, especially on the side of roads as supports for crash barriers, and the barriers themselves, would have longevity and maintain strength as they are water and termite resistant; a leading international sports shoe manufacturer is now using the recycled rubber for all its sports soles; wear-resistant floor surfaces for basketball courts and other sports surfaces; big pots for plants with longevity and resistance to corrosion; and also for the manufacture of solid tyres.
Published by
Focus on Transport
focusmagsa
