Ze fantastic ZF
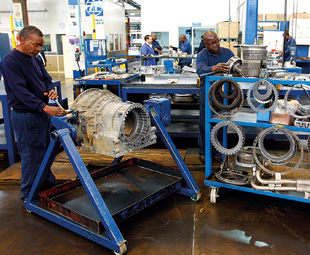
One of the world’s largest manufacturers of vehicle driveline components, ZF is taking its local business to new heights with impressive product and service offerings. GAVIN MYERS brings you the details.
Despite South Africa’s bus and coach industry being relatively small when compared to other nations, it is growing steadily. ZF offers driveline expertise for the bus and coach industry ranging from steering systems, transmissions, clutches and shocks, to the optimisation of complete drivelines.
ZF is also the leading supplier to Bus Rapid Transit (BRT) systems worldwide and is most excited about the BRT initiatives rolling out across major South African cities.
“ZF has an 85 percent market share in the BRT sector in South Africa,” says Derik Fourie, OEM general manager. “All 143 Rea Vaya buses are equipped with ZF Ecomat transmissions, while 24 MyCiti buses are equipped with ZF’s new EcoLife transmissions. In three years we’ve had no transmission failures on the Rea Vaya system, despite the very demanding stop/start conditions.”
With the introduction of ZF EcoLife (replacing the ever popular Ecomat) a host of advancements are on offer to operators and bus owners. The most significant of these is a fuel saving of 11 percent shown during a field test in Stuttgart.
Key features of this six-speed automatic transmission (designed to withstand input torques of up to 2 000 Nm) are: an integrated primary retarder with approximately 40 percent better braking ability than Ecomat; a 40 percent increase in service life and significantly extended service intervals; a newly developed torque converter with torsional damper for smooth uninterrupted gear changes; a reduction in fuel consumption; reduced noise emissions and ZF’s Topography Dynamic shift software (TopoDyn).
Ecomat with TopoDyn works on the principle of shifting between set shift programmes, pre-loaded in the software of the transmission. This enables the transmission to be in the correct shift programme for the current topography. However, TopoDyn Life (for EcoLife) is shift strategy software which enables the EcoLife transmission to variably adjust its shift vectors in a continuous fashion, enabling optimum fuel consumption and, as a result, increasing the average speed of the BRT bus. This means that TopoDyn has grown from being shift-change orientated to shift-adjustment orientated.
“We have also invested heavily in aftermarket support,” says general manager for technical service, F. X. Laubscher. “One of the elements of support is our Field service team consisting of eight highly-qualified technicians with fully-equipped vehicles and 24/7 availability. Our customers can, therefore, rest assured that professional assistance is only a phone call away. With the opening of a wholly-owned Cape Town branch, availability of technical support in the Cape region has also improved in the last year and we are seeing a steady increase in business in this region.”
Laubscher continues: “A product can be the best in the market, but if you cannot support it in the field it has a very low value for the customer.”
The company’s ISO 9001-accredited workshops in Johannesburg and Cape Town have also been upgraded with multi-million rand test benches to test reconditioned ZF transmissions, as well as the rest of the ZF product range, to ensure compliance with factory specifications.
The company also offers a number of service exchange units in case a transmission has to be replaced, reducing customer down-time significantly. Furthermore, a parts stock-holding of over R30 million, ensures that ZF gets customers back on the road in the shortest possible time frame. “In order to satisfy our customers’ expectations, our investment has been significant,” says Laubscher.
“All this is backed by a unique warranty package, demonstrating our confidence in our ability to provide customers with industry leading repair quality. Our customers know they are getting a transmission remanufactured to factory standards at a reasonable price,” he adds.
The ZF workshops are also accredited to test and recondition its Servocom steering systems. “These are safety-critical components. They shouldn’t be repaired by ‘Joe Soap’ due to the delicate nature of the repairs,” notes Laubscher.
With the solid foundation of a trusted company providing a well-established product and the focus clearly on customer support, what more could a customer
ask for?
Fourie elaborates on ZF’s association with the Southern African Bus Operators’ Association (SABOA): “ZF has been an active member of SABOA for the past 21 years and as the bus industry is a very close-knit community, we have made a lot of friends, met new business associates and
got to know the competitive environment.”
“We have changed our marketing strategy recently and are looking at different ways to market our brand and products. Customers can, for example, look forward to a ‘ZF drive day’. As of this year, ZF is also involved in the planning committee for the SABOA social committee,” he concludes excitedly.
Published by
Focus on Transport
focusmagsa
