Smooth going
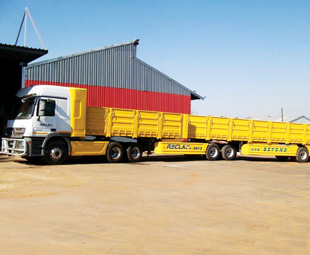
The household name in truck aerodynamics has a new home, and with it some interesting innovations. FOCUS visits Aero Truck’s new premises.
Twenty-seven years affords a company a lot of growth. As the biggest private manufacturer of aerodynamic equipment for trucks in South Africa, Aero Truck has certainly grown in leaps and bounds. Owner Cameron Dudley-Owen, who used to have to commute between the aerodynamics and bull bar factories which were 80 km apart, realised the need for expansion earlier this year.
“We needed more space and so we bought premises in Alberton North that were not only bigger, but also allowed for future expansion,” he says. Both factories were merged, with the new premises being divided into a dedicated aerokit moulding facility and an adjacent metal-working facility – where the bull bars and frames for the kits are fabricated.
The new workshops allow for approximately six trucks to be worked on at any given time, despite the fact that most fitting is still done at customers’ premises or at the company’s Durban and Cape Town branches. The operation now benefits from greatly streamlined administration, design, manufacturing and (where necessary) fitment processes.
With the expansion of its facilities, the company is also moving into some new and novel areas of vehicle aerodynamics. The first of these are units belonging to scrap metal recycling group Reclam. The vehicles, Mercedes-Benz Actros and Axors, haul scrap metal from inland regions to the coast. These vehicles, though, are not fitted with just any old kits.
“The kits differ considerably in that they close the gap between the horse and trailer. The cab extenders are much longer and, although the roof stays at the same level, it too is extended to match,” says
Dudley-Owen.
Modifications were also made to the rear of the trailer, including an upper and lower diffuser to duct the air into the vacuum at the rear of the vehicle. “This rear vacuum accounts for about 15 percent of drag, which is reduced, but not eliminated,” Dudley-Owen points out.
By closing the gap between cab and trailer – and between the trailers – airflow is streamlined along the length of the vehicle, reducing turbulence and wind separation. This is also true of the chassis panels which channel the air under the trailer as well as along the sides, thereby minimising wheel turbulence, Dudley-Owen explains.
The company is pushing even greater boundaries, however, on behalf of car-ferry company VDS that came to Dudley-Owen with the idea of building a mechanically adjustable kit for its vehicle transporters. The theory was that it needed to be easily adjustable to maximum height when the vehicle is loaded, and to its lowest height when unloaded.
“Reduced fuel consumption would only be possible if the frontal area could be reduced for empty return trips,” he points out. “It is true that car transporters are not particularly aerodynamic, but as 80 percent of drag occurs at the front of the vehicle, we would expect some gains.”
The concept could also be suited to other applications such as flat-deck trailers carrying containers. “When kits are not easily adjustable, the driver is unlikely to bring them down when unloaded. Our new system could remedy this situation,” Dudley-Owen notes.
Unfortunately, until more distance is clocked up by Reclam and VDS, the extent of the gains that can be achieved, remain to be seen. But with innovative projects like these and new premises to make them a reality, Aero Truck is looking forward to a streamlined future like never before.
Published by
Focus on Transport
focusmagsa
