The fresher, the better
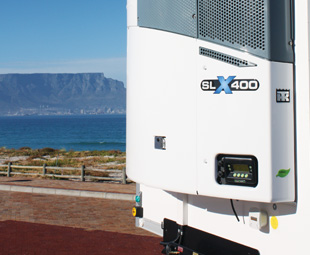
A difference of just 1°C can reduce the shelf life of lettuce by more than a day – demonstrating just how powerful and important refrigerated transport is. No wonder the industry is alive with innovation, as JACO DE KLERK reports.
“Sunny South Africa” – ours is a climate many foreigners envy, but glorious summer days and even sunnier winters present the refrigerated transport industry with some serious challenges.
As Clinton Holcroft, MD of Serco Industries, a leading manufacturer of truck bodies and trailers, says: “Ambient temperatures are high in our country, so thermal properties need to be good if the integrity of perishable goods is to be maintained.”
Serco uses high-density polyurethane insulation to ensure that its units have excellent thermal properties, and laminated exterior fibreglass skins for food products that require a hygienic interior surface.
Temperature control
But insulation is futile without a means of temperature control. One company addressing this need is GEA Refrigeration Africa, provider of Thermo King temperature control equipment in South Africa.
“We sell the complete range of Thermo King refrigeration equipment,” says Ronnie Meechan, general manager of the transport division at GEA, adding that three market segments are catered for: trailers, rigid tucks and vehicle-powered units.
“The SLX400 for trailer applications is our flagship product,” he says. “We’ll be launching the second generation model later this year.” Close on its heels is the SLX Spectrum, a multi-temperature unit also used for trailer applications that has gained significant popularity in the last two years.
“In the rigid truck range, we have a variety of units depending on the size of the box and the application,” he continues. “The T-series is the best in its class with regards to fuel consumption and capacity ratios. The MD100 Dairy unit is also specifically designed for high capacities in fresh applications and will soon be replaced by the T500 Dairy, which has even better specifications in the same price range.”
For smaller vehicles, there’s the V-series, which has a cooling range from nought to -25°C depending on the application, demonstrating that GEA covers a wide range of refrigerated transport requirements.
Ongoing development
According to Serco’s Holcroft, innovation and development in this sector ongoing. “Transporters are looking for improved durability as well as more cost effective units, so there’s a lot of pressure to innovate,” he says. “Going green is also a growing area of interest that we’re looking at.”
Meechan adds that there’s a trend towards refrigeration units that ensure a sustainable decrease in CO2 emissions and noise pollution. “Thermo King is at the forefront of this,” he says. “The company has developed conventional diesel units that are PIEK-certified – this is a European standard that requires diesel motors to limit pollution and keep noise below
60 decibels.”
The company has also developed a cryogenic unit that uses CO2 generated by other processes as its fuel for temperature control.
These units, called CryoTech systems, move liquid CO2 from a refillable vehicle tank through a sealed evaporator coil inside the cargo space. Temperature-controlled air is circulated over the coil and through the cargo space and then, having extracted all the useful cooling energy, the CO2 vapour exhausts into the atmosphere – leaving the cargo space completely.
Because the liquid CO2 is sourced from recycled waste gas, there is no contribution to global warming from the CryoTech’s release of carbon dioxide vapour into the atmosphere. The systems enable a second use of the substance and ensures that no additional greenhouse gases are created during the process.
The total carbon footprint for the use of a CryoTech system is a quarter of that of a conventional diesel system and a third of a nitrogen cryogenic system. CryoTech systems also meet the PIEK standard, generating 90 percent less noise (at its loudest) than a conventional diesel refrigeration unit.
Plus, its cooling capacity doesn’t change with ambient temperatures since it doesn’t use a condenser coil. These units can also pull down and recover temperatures up to four times faster than conventional systems. This ensures that ambient air entering the cargo space during each delivery is dealt with quickly – making these systems ideal for South Africa.
More than 200 of these units are running in Norway, with a growing number being fitted in the Netherlands. “We are currently in discussions with two major retailers to run a few units in local conditions to analyse the cost implications and establish viability,” says Meechan. He adds that the purchase and installation costs of CryoTech systems are similar to other units, with lower maintenance costs being recorded in overseas markets.
However, as Holcroft points out, our country’s operating conditions are often more harsh. Some South African roads are in appalling condition, and we have a huge dependence on road freight transport. This combination wears on both the vehicles and units used to transport goods. “The units and truck bodies need to be able to withstand heavy wear,” says Holcroft. “Operators also often subject the bodies and the towed units to harsh conditions during loading, so the units need to be able to withstand pallet jack operations.”
Impact on shelf life
Regardless of the operating conditions, it’s essential that temperatures are monitored since even small variations can significantly affect the shelf life of produce. To illustrate the point, a difference of 1°C can reduce the shelf life of lettuce by over a day, while grapes deteriorate more in 10 minutes at 35°C than in 16 hours at 20°C.
Serco has stepped up to address the need for monitoring through its marketing and promoting of Ikhaya Real Time Temperature Monitoring Systems. Gareth Curtis, operations manager of KLL Distributors, says he chose Ikhaya because he needed a system that could provide real-time temperature readings as well as historical reports – which he can give to his suppliers to assure them that their products are in good and safe hands.
KLL is a third-party multi-temperature warehousing and logistics business operating from seven centres around the country. It has 5 000 racked pallet spaces, of which 3 000 are temperature-controlled. The company has installed the Serco-backed Ikhaya system onto all of its freezers and chillers, including its fleet of 15 trucks.
Curtis says the system has numerous benefits since it is Internet-based and can be logged onto from anywhere to see what the various units’ temperatures are. This allows for constant assessment and enables immediate intervention should problems arise or potential problems be foreseen. “The SMS alerts are a huge asset, giving us peace of mind that the freezers are working at any time of the day or night. And we can customise the alerts to inform us of any changes in temperature as an early warning system so the products’ integrity is maintained
at all times.”
The system could also be very beneficial with regards to the Consumer Protection Act because it provides operators with a means to prove temperature traceability in the event of a dispute. “We can also go back and track a previous day’s route to verify the validity of any complaints from customers about the in-vehicle temperatures,” says Curtis.
The system is also helpful in managing staff. “I can now can see if they are using a vehicle’s freezer unit correctly to ensure the cold chain is maintained at all times.”
Roll-up doors
Another product Serco distributes that helps to maintain the cold chain while providing additional benefits is the TS 50 Safeguard roll-up door from Whiting. Roll-up doors are ideal for use in congested areas where side room is restricted, and can be used with any kind of tail lift.
Serco’s Holcroft says these doors are popular in the US and Europe because they’re easier for truck drivers to handle, make docking simpler and improve security since the truck doesn’t have to be moved before the door can be closed and locked – ensuring that drivers actually do this. The doors also suffer less damage during docking than conventional barn doors.
“There are also advantages for drivers since they don’t have to get in and out of the vehicle several times when docking to hook and un-hook the back doors,” says Holcroft. “With roll-up doors, a vehicle can be reversed right up to the dock before being opened for loading. Thereafter, the doors are closed, secured and the vehicle can be driven off when ready.”
Whiting is a leading supplier of roll-up doors for the transport industry, and has selected Serco to sell its products with the aim of growing its market. With its TS 50 Safeguard roll-up door, insulation is greatly enhanced thanks to the use of a 50 mm polyurethane foam, which is CFC-free, while its dual-durometer top seals further enhance thermal performance. The door is robust, with stainless steel shafts and hinges, and has a 1,78 mm aluminium ribbed extrusion inside and out.
Low noise, “piek” performance
In 1998, the Dutch Government set out standards for noise emission during loading and unloading in retail trade and craft businesses. This resulted in a project called PIEK and led to the introduction, in 2004, of the PIEK certification scheme for vehicles and equipment operating under 60 decibels that will be suitable for use in night time deliveries without causing noise disturbance. The PIEK standard has been adopted in several countries, including the UK, France, Germany and Belgium.
Published by
Focus on Transport
focusmagsa
