Towing the load
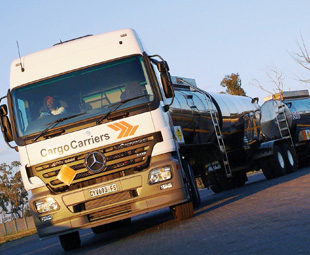
GAVIN MYERS joins with industry players to explore the state of the South African trailer market.
In the world of trucking, the “big numbers” are what usually attract our attention. After all, it’s the truck tractor (and/or chassis cab) – with its large capacity, high horsepower and multiple-axles – which is the driving force and mover of loads across the continent.
But without trailers, tankers or refrigerated units (hereafter collectively referred to as “units”) in tow, not much would be moved around at all. These units are the unsung heroes of the trucking world, with few people stopping to think about their design, innovation, cost or efficiencies.
So, what are challenges of acquiring, insuring and maintaining the right unit for the job? Can it stand up to the tough operating conditions and tasks required of it? If not, why?
Unfortunately, certain industry players – notably those in tanker manufacture and supply – declined our invitation to participate in this feature or did not respond. However, we feel the responses we did obtain are fairly representative.
A complex industry
Local companies like Afrit and Serco have been in the business for decades, with several newer and smaller trailer builders also now making a name for themselves. Others, like the GEA Group (refrigerated transport), import directly from overseas suppliers.
But units designed and built in South Africa are up to world standards and often surpass them. Seemingly, we only fall behind on the quantities of trailers built and supplied.
“Our designs are comparable with what is available globally; however, trailers need to be designed to suit local conditions,” says Clinton Holcroft, managing director of Serco. “South Africa has very harsh operating conditions and some foreign products do not stand up. Reparability can also be a problem with foreign products.”
Designing a trailer can take anything from one or two weeks, to a month or more. Depending on requirements, features and design aspects, trailer manufacturers will typically take into account things like whether the product is standard or has unique features, the payload and/or volume required, and the client’s preferred truck tractor.
It is important to understand the client’s unique requirements and expectations. In refrigerated trailer design, it is also vital to consider cooling capacity, airflow and diesel usage – all of which combine to affect the rig’s efficiency.
Leon van de Wetering, Afrit sales manager, says the company’s designs focus on several key requirements: reducing trailer mass in order to deliver the maximum payload; ease of manufacture so as to reduce product cost; and maximising robustness to ensure good service life.
In terms of service life (taking into account design and application), a well maintained and properly-treated unit should last a minimum of eight years, going up to about 15 years. Holcroft advises that durability is critical and so, in the long run, “cheaper” is often anything but.
However, he says it is also up to operators to properly maintain the trailer and body, as well as to train their drivers (and, in many cases, themselves) to also avoid abuse of the equipment – something which is a problem across the board.
Holcroft is passionate about solving the problem of abuse. “Operator abuse is high. For refrigerated trailers this is particularly evident when loading vehicles with motorised pallet jacks, which can cause unnecessary damage to interiors,” he warns. “Availability of quality drivers is also a problem. Due to shortages, poor drivers can move on to other transporters and regulations are not strict enough to weed out the unsafe ones.”
Refrigerated units themselves should last for around seven years, almost tying in with the trailers on which they’re constructed, advises Ronnie Meechan, general manager – transport at GEA Refrigeration Africa (Pty) Ltd. “Customers are looking for maximum payload, high durability and ease of repair during the life of the trailer. This is critical to the success of the transporter,” he says.
“Downtime and penalties for overloading can kill a transporter’s business,” he adds, “while obstacles like low-hanging branches in urban areas often cause damage to the exterior of refrigerated trailers.”
With all these hazards, how can you ensure the unit will be dependable, long-lasting and efficient? Again, it comes down to design; a trailer’s longevity depends on the strength in critical high-impact areas such as the side walls and floor.
Manufacturers are also careful to use superior, reliable material bought from dependable suppliers when constructing their trailers. “But using superior materials will not help if the design isn’t done properly,” emphasises Van de Wetering.
If the design is completed correctly, and maintenance and abuse levels are kept in check, the unit should have an extended working life and be able to move from owner to owner.
There is certainly a market for used or rebuilt units, which can often be as good as new if rebuilt correctly and without taking shortcuts. The problem that builders like Afrit, Serco and GEA find, is that many operators undertake little or no maintenance, leading to too many unroadworthy units. According to Holcroft, a particular – and worrying – area of concern is braking safety.
As regards refrigerated trailers, Meechan is keen to also point out that rebuilt units are often as reliable as new. While they naturally have a shorter lifespan, the risk can be mitigated by using a reputable supplier who provides a full warranty (GEA, for example, is one). With refrigerated units, stripping and reconditioning them with new engines and compressors should be the order of the day.
Strangely – considering the bleak track record of operators when it comes to poor maintenance and abuse of their units – Van de Wetering, Holcroft and Meechan all mention aftersales and support services as one of the most important factors that customers take into account.
From the operators’ perspective
Considering that a company like Imperial Logistics, for example, has 2 485 trailers and approximately 1 750 tankers in its fleet, you would expect technical and fleet managers to be reasonably well informed when it comes to the units that effectively carry their business. So it’s interesting to find that what the operators say is, in some cases, at odds with the manufacturers’ viewpoints.
Francois Ehlers, Imperial Logistics technical director, and Peter Watts, Imperial Logistics Specialised Freight technical director, say many inferior components find their way into the local trailer market as a result of manufacturers trying to be price competitive. “This becomes a safety risk, which in turn generates high maintenance and cost per kilometre (CPK) costs,” they say.
This can also be due to fault on the operator side. “Quality components in trailers produce the best numbers when it comes to safety, maintenance and CPK costs,” say Ehlers and Watts. “However, a major problem arises when you do not specify, by name, the components required. More often than not, cheaper, inferior components are (then) used by the manufacturer.”
Quality is therefore a non-negotiable for an efficient fleet of trailers – low maintenance and CPK, minimal downtime, durability, reliability and high payloads are the results operators expect. A safe fleet is also an efficient fleet, and safety-critical items are crucial in trailer design – in particular the braking system, fifth wheels and tow hitch equipment, say Ehlers and Watts.
Tankers, albeit subject to these same safety-critical parameters, can pose a greater headache than their basic trailer counterparts. This is because payload is even more important, and also because tankers usually need to be purpose-built, according to their specific operational conditions and the products intended for transportation. As a result of this, specifications differ substantially from unit to unit.
“Dangerous goods (DG) tanks are very different from food grade tanks,” notes Watts. “With tankers generally being purpose built, you seldom find units for sale ‘ex stock’. You can therefore specify the extras according to the intended operation.”
Piet Potgieter, general manager – technical at Cargo Carriers Ltd, concurs. “A big challenge in the chemical industry is to have tankers that can transport the majority of the chemicals. Another challenge is to build tankers which are as light as possible, especially cladded tankers.” Potgieter says that some of the biggest inhibitors to running an efficient fleet of tankers are: tyre wear and scuffing in city traffic; lack of technical support in rural areas and neighbouring countries; poor road conditions which result in chassis failures; and the costs of valves and offloading equipment.
Considering the cost of purchasing and running a fleet, it’s easy to understand all the frustrations. While purchase prices will depend on the specification and type of unit, chemical tankers have an average price tag of around R800 000, fuel tankers cost between R1 million and R1.5 million (depending on length and accessories), a DG combination comes in at approximately R1.4 million, while a food grade combination tanker can cost around R1 million.
Maintenance and running costs vary between 18 and 70 cents per kilometre, while insurance costs are pegged at around 4% of the original unit price.
Where, then, does that leave second-hand/rebuilt units? Despite the manufacturers’ view that a properly rebuilt trailer can be as good as new, the operators are weary. Possibly the biggest problem with older trailers is that they are heavier than newer designs, which affects payload efficiency.
“As a rule, Imperial Logistics does not purchase used and/or rebuilt trailers,” says Ehlers. “The fact is that we will replace a trailer because of a deficiency. In very select cases, rebuilt tankers may be considered, however the rebuild would have to have followed the very specific design codes required for a new vehicle.”
Of course, tankers present their own set of complications. “The rebuilding of tankers is not always an option,” says Potgieter. “With stainless steel tanks that were used to transport chemicals like ANS and ANCN, you will have problems with metal fatigue, because these products are loaded at 130°C. Aluminium tanks also start to crack after some years of service.”
Developments and the SA market
Unlike the Europeans, the South African market is unique and has different requirements. Meechan notes that Europe comprises mainly owner-operator fleets, where our drivers and owners are paid a salary. In South Africa there is still the thorny issue of poor legislation and slack law enforcement, both of which negatively affect the industry. “A challenge particularly impacting tankers is the lack of government enforcement regarding DG legislation,” adds Watts.
As a result of these unique elements, trailer designs often change to accommodate the needs of the industry, This, according to Van de Wetering, poses a challenge for builders. “It would be better if we could manufacture only a couple of standard products, like in Europe and America,” he says.
But, note Ehlers and Watts, South African trailer manufacturers generally compare favourably to global manufacturers. New local and international innovations are finding their way into our market, among them: electronic braking systems offering improved safety; on-board weighing systems to avoid overloading; rear park distance control devices to reduce docking damage; real-time temperature monitoring devices for refrigerated loads to maintain the cold chain; and cryogenic units which are designed to reduce the carbon footprint caused by diesel usage.
Van de Wetering is excited about Afrit’s new flatdeck trailer that also allows the option of bulk loading. Holcroft says Serco’s new roll-over doors are proving their benefit, as are temperature-monitoring telematics systems and a new trolley strapping system.
It’s clear the operators take their units seriously and, as such, the trailer builders are motivated to innovate and improve in order to meet their needs.
Undoubtedly, in the world of trucking, the trailer is truly the unsung hero.
Published by
Focus on Transport
focusmagsa
