Driving supply chain improvements
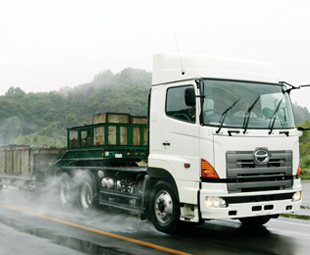
As someone who has worked with many diverse companies over the last 10 years in the role of a supply chain service provider annually scrutinised for cost reduction, improvements and strategic solutions, ALYDA LE HANE of the Supply Chain Council has personally been in the spotlight to deliver against one, if not all, of these requirements. This dilemma is neither unique nor isolated, she writes.
Expecting results from a single party in isolation reminds one of a teenager setting the rules in the home without the support or understanding from the parents in question, with similar catastrophic results.
Solutions are frequently demanded from the logistics manager whose role is just that – logistics. Unsurprisingly, the logistics manager’s intervention will naturally emanate from within those confines, i.e. logistics.
Like the parent, the executive, once aware, is not often in favour of the isolated decision given their understanding of the impact on the total supply chain. The inevitable questions then arise: Where is it? Why is inventory so high/low? Why are the associated costs so high?
With respect, the logistics manager has taken decisions from within the realm of his/her knowledge, responsibility and accountability.
A recent example to illustrate the above involves a global organisation that needed to drive down cost to its branch in South Africa. An incumbent person very conscientiously investigated the cost of containers and discovered that the utilisation of pallets in containers eroded 30% of the available space. Rightly, they instructed their expediting office to no longer use shrink wrap on pallets, but hand pack containers with product cartons.
Objective instantly achieved: a 30% saving of cost of container.
Let’s put numbers to this in order to understand the quantified value at the unit level, i.e. one equivalent unit (TEU) 20 ft from somewhere in Europe. The cost of the TEU is approximately $1 500 (R12 300); a 30% saving amounts to $500 (around R4 100).
What should have occurred is a discussion with all the stakeholders at least within the four walls of the organisation, if not the end-to-end supply chain. First consideration should have been given to the nature of the product, i.e. an over-the-counter pharmaceutical product, packed in bottles. The requirement would be to effectively deliver to the retailer, which requires that the product be delivered in its manufacturing batches and according to expiry dates.
In this example, the reality unfortunately played out differently. When opening the container doors for destuffing and unpacking, the product fell out (owing to the movement that occurs in a container on the water). Immediate waste (and mess due to the liquid nature of product) was approximately 5%.
The calculation is now at the product level, which in this instance was R500 000 value per TEU. Five per cent represents R25 000. Consequently, the trade-off is between 30% saving of container rate (R4 100) to 5% of damaged product at R25 000. The immediate loss in this equation is R20 900, plus additional incurred costs to sort cartons into their respective batches and according to expiry date.
The cost of the decision to hand pack containers should have included product waste, resources to sort for bulk packing and distribution, additional lead time, and so forth, Notwithstanding that this product is sold into the retail environment with the accompanying cost associated with late delivery, reducing rate of sale and so on.
There are many other examples that include moving product to Gauteng distribution centres without understanding the end-market consumption.
Why haul products to Johannesburg only to redistribute in large quantities to Durban? A classic example involves the distribution of generic medication for a disease that occurs primarily in KwaZulu-Natal, but the medication is always in short supply. The distribution of this product commences in the East where it is sourced, brought through the port of Durban to a distribution centre in Gauteng. There the container is unpacked and the major portion then redistributed back to Durban. This flow creates an additional lead time of 10 days, compared to breaking bulk in Durban. The validity of said product unilaterally following the process of other product categories is clearly in question.
It would be more effective to break bulk of the container in Durban, deliver directly to the local channels and then transport the balance to Johannesburg. The value would be improved customer service, reduced lead times, improved cash to cash, reduction in shrinkage and loss and reduced distribution costs.
There is much efficiency through the use of distribution centres. However, given the impact of technology and new methods of distribution and sales – such as merge-in-transit, cross-dock and vendor-managed inventory – the decision of managing a supply chain should be driven by the product, its channels and the end user.
Several methods for driving strategy in an organisation exist. However, if the metrics that “sustain” the competitive nature for a given product have been the same for the last number of years, it is likely that comprehensive understanding of the nature of the product-driven supply chain is compromised. There will be many executive requirements, but very few end-to-end supply-chain-supporting actions.
The Supply Chain Operations Reference-model (SCOR), developed by the Supply Chain Council, has a proven process that focuses on strategy for each product/service-driven supply chain. SCOR develops an understanding of the “as is” to ensure that the desired state or “to be” is driven by current best practices. In turn, this ensures market leadership and supply chain sustainability.
The outcome of a SCOR initiative will deliver a portfolio of prioritised and articulated supply chain projects. In addition, the process will clearly define the metrics required to sustain the desired competitive performance.
The implication is that strategy has a direct impact on the metrics that need to be in place with each phase of the product lifecycle and the supply chain delivery of product to market. Post strategy, the clarity of definition and significance of required metrics will ensure that lean and Six Sigma initiatives will be supporting the organisational strategies per supply chain.
Expecting a logistics manager to drive supply chain improvement without end-to-end supply chain engagement is naïve at best. The logistics manager should implement and execute against the executive product supply chain decision. If not, cost-saving initiatives will sabotage the ability of getting product to market. The key to product supply chain sustainability depends on the clarity of vision at the executive level among all enterprises engaged in delivering the product to the consumer. In this context, SCOR articulates the plan function, i.e. P1 = Plan the Supply Chain.
Someone once said: “…in the past, your business had a supply chain; today your supply chain is your business.” Reality indicates that every business has many supply chains; the deaggregation of supply chains from an amorphous complexity of functions into clearly defined strategy per product grouping will enhance an organisation’s ability to compete in their markets with sustained success.
Published by
Focus on Transport
focusmagsa
