Feast of innovations
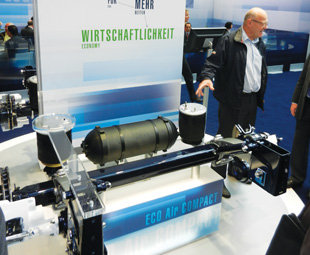
Food on the one hand, and trailers, axles and suspensions on the other, don’t normally go together. But as Andre Cilliers, managing director of BPW Axles in South Africa, was proud to point out, the company was not “serving any warmed-up meals” on its IAA stand. Instead, as CHARLEEN CLARKE discovered, freshness was the order of the day …
Everything is brand spanking new. That’s what Cilliers meant when he made the reference to “warmed-up meals” – or rather, the lack thereof. At exhibitions, we are sometimes served up “face-lifted” products; displays that (yawn) really don’t demonstrate anything new.
But that certainly wasn’t the case at BPW Axles’ extremely busy stand this year: there wasn’t an old or face-lifted product in sight – visitors were treated to a feast of trailer, axle and suspension technology innovations, as the following highlights show.
COMING SOON TO A TRAILER NEAR YOU?
My personal highlights were two futuristic concepts: the ECO Vision (a plastic axle) and ECO Vision E, a concept study showing energy recovery on a trailer.
First, a bit of detail on the axle, which is designed for axle loads of up to nine tonnes and disc brakes. The configuration as well as the installation and operating specifications are in line with the current specifications for conventional air-suspension systems.
I am, perhaps, oversimplifying the concept somewhat when I state that it is made from plastic instead of normal steel. The axle beam of the ECO Vision is made from glass fibre-reinforced plastic (GFRP) which is, of course, a lot more sophisticated than just plain plastic. “Today, conventionally built air-suspension modules weigh at least about 400 kg. ECO Vision weighs 320 kg, which amounts to a weight reduction of about 20 percent,” said Cilliers.
But is it strong enough? “Absolutely,” stressed Cilliers, “it’s incredibly strong. This composite material, which is made from polyester resins and glass fibres, is even stronger than steel. In addition, it’s highly resistant to corrosion, weather and chemicals.”
The design of the GFRP air-suspension module combines mechanical advantages and material resilience with significant weight reductions and obvious visual benefits.
ECO Vision is not without its challenges – for one, as Cilliers points out, production of the unit would be very labour intensive and time consuming. But it’s an incredible concept which, not, surprisingly, was awarded the Trailer Innovation Prize at the fair. Take a well-deserved bow, BPW!
The second futuristic concept is equally clever. We’ve all heard about energy regeneration on vehicles – but what about trailers? Well, the clever chaps at BPW – in conjunction with the University of Bremen – put their collectively very clever heads together and came up with ECO Vision E, which does just that.
So how does it work? “Essentially, we took generators and installed them in both hubs of the ultra-light GFRP axle,” explained Cilliers.
The surplus energy that is generated (as much as nine kilowatt hours) is stored in a battery – and can be used to power customer-specific electrical components such compressed air system for the air suspension and cooling units.
“This power could also be used to assist the engine – with resultant fuel savings,” said Cilliers. “We reckon that fuel savings of one to two percent could result.”
BPW, I reckon that’s worth yet another bow …
COMING TO SA: ECO AIR VARIO
Of course, those are both futuristic concepts – hopefully they will come to South Africa one day. But one concept that WILL come here is the ECO Air VARIO trailing arm. “I love this concept because it means we will be able to offer a single suspension range for all applications, from nine to 14 tonnes,” noted Cilliers.
As we all know, it’s definitely not normally a case of “one size fits all” when it comes to suspensions and commercial vehicles. But that’s what the ECO Air VARIO trailing arm concept achieves. “It’s a modular system, which also reduces the weight of the air-suspension,” Cilliers explained.
This is big news: in transport, of course, every gram of weight counts. “By using ECO Air VARIO, hauliers will achieve weight savings of about 10 kg per module. If required, the weight can be reduced by a further 20 kg using an optional aluminium package. This means the entire module weighs only 370 kg, depending on the configuration. It is an advantage that has a direct pay off,” Cilliers noted.
In typical BPW fashion – “We have a saying within our company that people believe everything revolves around axles, but actually everything revolves around customers,” Cilliers noted with one of his characteristically huge smiles – maintenance of the ECO Air VARIO is ever so easy. “The individual parts can be replaced quickly and easily, which ensures particularly low operating costs,” said Cilliers.
ECO Air VARIO will be introduced in Europe in 2014; Cilliers believes that “we won’t get it before 2015 because of all the testing that will still be done”. Sounds like it will be worth the wait.
SELF-STEERING AXLE: NO LUBE NEEDED
Self-steering axles are, of course, not new to BPW – the company has been in the market for some time, and has clocked up impressive fuel savings of the order of three percent! But the big news at the IAA was the new ECO Turn self-steering axle that doesn’t require lubrication.
How has this been achieved? “We are using steel-rubber-steel bushes, which are absolutely maintenance-free and have very high life expectancy. At the same time, when repairs are necessary, the steel-rubber-steel bushes can be exchanged with ease,” revealed Cilliers.
And, as they say in direct marketing commercials, that’s not all. Another advantage of the new system pertains to weight, which could be reduced by up to 10 percent.
And all the other advantages of self-steering axles still apply. Due to the fact that each axle undergoes significantly lower tyre side forces, it has been shown that there is a 50 percent increase in performance with the front axle, and as much as 70 percent with the rear. “Also, these axles allow for the lighter construction of frames, which means a reduced trailer weight and an increased payload,” explained Cilliers.
With these self-steering axles, operating costs are significantly reduced: over a distance of 100 000 km, up to four tyres and 1 000 litres of fuel can be saved. Road damage is also reduced – vastly.
LEADERSHIP DEMONSTRATED
There were a number of other fascinating new products on display – the ECO Tronic TCONTROL telematics, with integrated tyre pressure monitoring; a new BPW Mobile app; the new ECO Air COMPACT running gear system with a completely newly developed air-suspension and innovative, lightweight air tanks; and ECO Wheel aluminium forged wheel – all proudly displayed under the joint theme of “Let’s go ECO!”
Needless to say, the stand was a constant hive of activity. The innovative company – founded in 1898 by the Kotz family, which owns it to this day – did a terrific job of luring customers from all over the world. In fact, the BPW stand attracted 50 percent more visitors than it did two years ago, and it was particularly interesting to see the prevalence of Russian and Turkish visitors.
Cilliers said the reason for the busy stand was simple: “BPW is the leader in trailer, axle and suspension technology; this is where visitors are coming if they want to see the very latest technology within those fields,” he pointed out.
I could not have phrased it better myself.
Published by
Focus on Transport
focusmagsa
