Rehab rising?
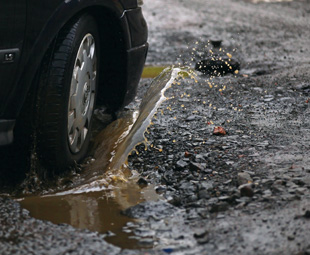
With South Africa’s ailing road infrastructure, road rehabilitation should be on the cards of most municipalities. GAVIN MYERS attended the 2013 Southern African Transport Conference where he got insight into an exciting new way to do this.
Gridlocks, thousands of vehicles in all shapes and sizes, pedestrians and a crumbling infrastructure, make road maintenance a non-negotiable for municipalities. For a multitude of reasons though, South Africa’s roads agencies have been slipping somewhat in this regard.
Some of the most pertinent reasons are: the high costs involved, the long time to completion, the need to divert and work around traffic and the sheer amount of work to be done. But, for the inner city at least, speed, price and quality need not be exclusive – there is now an innovative, quick, inexpensive (relatively) and high-quality option to fulfilling road rehabilitation needs.
The process basically involves placing a stabiliser grid directly under the bitumen (these grids are usually installed much lower down), with no need to replace the lower layers of the road. A project undertaken in Bloemfontein was unique in that it was the first time this process was used to rehabilitate a road. The roads were Harvey and Hanger in the Bloemfontein central business district. The N1 north and south, N6 and N8 all lead in to and out of these roads, which are made up of two to four lanes and seven to eight intersections.
The challenges presented by the location of the roads, and subsequent need for a quick and simple process, are therefore fairly obvious. Says Vonda Pretorius, specialist at the Bloemfontein Royal HaskoningDHV: “There were thousands of pedestrians, and a huge number of buses going in and out every day bringing people from the nearby townships, as well as heavy traffic and an inter-modal transport facility right there. Our construction work needed to be as shallow as possible for pedestrians to cross over dug-up sections and ensure cars wouldn’t fall into the excavations if there was an accident.
“Yet another challenge experienced was the utility services – we couldn’t rehabilitate around all of them. The roads had poor and insufficient subgrade layers that had been there for many years and had been tightly compacted by traffic. There was also a high degree of variation between the pavement structures at the intersections. All this had to be incorporated into the design. Further, construction time was critical and natural environments also needed to be considered with as little material used as possible. The shallower the rehabilitation of the road the better,” she notes.
A visual inspection revealed crocodile cracking, broken surfaces, degraded potholes and patches. The roads were not badly rutted though. Pretorius says that traditional road rehabilitation of deep pavements goes hand in hand with reconstruction or partial reconstruction of the pavement, strengthening of some of the layers, and applying asphalt and granular overlays and surfacing. “If we had to do this pavement using traditional methods, it would involve excavation, reconstruction, graders, rollers and tippers for each layer. It could create more problems if we had to excavate.” It could also have taken up to 46 days to complete a section … .
So how exactly were all these challenges overcome? “We had to have a pavement design strong enough to carry all the traffic. Our construction level was fixed between the curves and we had to construct short sections at a time, using good material and an easy construction method,” Pretorius notes.
The first steps were to mill out the asphalt and then the existing base to a nominal depth of between 124 and 190 mm depending on the section of road. The milled-out asphalt was then used as reclaimed asphalt in the new base, and the removed base was stockpiled for other use by the municipality at a later stage.
From there the existing lower layers were treated before the mechanical stabiliser was put in place. “This was to compensate for the inferior lower layers,” notes Pretorius.
The bitumen stabilising material was then paved directly onto it and, thanks to the use of the grid, the required thickness of the layer was also reduced. “This is where the old and the new technology were combined. Paving the bitumen directly onto the stabiliser hasn’t been done before,” she smiles. “With the correct rollers and graders we got a smooth surface with the correct compaction density.
“We undertook a full and proper design analysis and, therefore, are comfortable with the design,” Pretorius emphasises.
The results were an amazingly short construction time of just twelve-and-a-half days per section, after which the completed section could be opened to traffic within three hours. The project was finished well in time and within the budget of R22 million. With the remainder of the budget, the team was also able to rehabilitate an additional 435 m of road.
What causes road damage?
Morris de Beer of the CSIR Built Environment explained causes and types of road deformation and damage and emphasised the interaction between tyre inflations and the vehicles’ mass with the road surface.
“This needs to be known in road design,” he says. “Most failures originate at the top of the pavement where contact stress plays a major role. We need to know how to avoid these things.”
With various types of fibre in our roads, De Beer emphasises the need to get rid of vertical and horizontal movement of the asphalt, cracking, potholes, delamination, surface disintegration and water. “Water is the cancer of pavements – if you combine water and load, you will have a very sick pavement,” he emphasises.
De Beer and two colleagues have been examining the interaction between tyres of various pressures and loads with the road surface, using Stress in Motion (SIM) technology in controlled and field tests.
SIM technology gives a better idea of a rolling tyre’s interaction with a course surface, capturing 3D tyre force (downwards, forwards and backwards and side to side) on the road. “A tyre print isn’t circular as often thought; it’s more rectangular, depending on load and tyre pressure. Every tyre has a unique print,” he says.
With an understanding of the interaction from controlled tests, an uncontrolled study was done with random trucks at the Heidelberg weighbridge. “The tyres fitted to a vehicle are supposed to be the same but were often found not to be – differing inflations, new and old, different loads, and the like were often recorded.
“The shape of tarmac deformation relates to the input stress from tyres. Overloaded or under-inflated tyres are not healthy for the tyre or pavement,” he says. This is because the edges of the tyres become over stressed or under stressed. “Inflating the tyre higher gives peaks in the centre, but when the vehicle is loaded legally it gives the required forces on the edge of the tyre to balance out the footprint. Understanding this interaction is essential for longevity of the pavement,” he concludes.
Published by
Focus on Transport
focusmagsa
