Sick and tyre’d of pollution
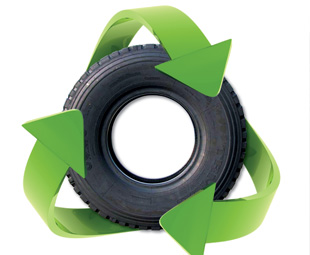
Tyres are a serious recycling and waste management problem – even with current know-how, we still haven’t found an economical way to recycle them. FOCUS investigates what can be done.
Twenty-one-million – that’s how many tyres South Africa has to deal with annually, both new and used, according to the Recycling and Economic Development Initiative of South Africa (Redisa).
It’s alarming to think that with no real economical or sustainable way to recycle them, that most of these tyres are sitting in the veld and dumpsites around our country.
Landfill sites aren’t accepting tyres for two reasons: firstly, they cannot handle the capacity; and secondly, because the groundwater is slowly being polluted by the tyres that are already lying around. In addition, people are illegally burning tyres to reclaim the steel wire within – creating huge clouds of noxious acrid smoke.
As previously reported in FOCUS, the Department of Environmental Affairs (DEA) received three proposals for its Integrated Industry Waste Tyre Management Plan – from Redisa, the Retail Motor Industry Organisation (RMI) and the South African Tyre Recycling Process Company (SATRP).
The Redisa plan was approved, but there has been much controversy surrounding its implementation. The DEA selected the Redisa plan largely because of its promise to promote social responsibility within South Africa by creating jobs – but both SATRP and the RMI have voiced concerns over the plan, and both for different reasons.
Many others in the industry have too voiced their disapproval of the Redisa plan and in conjunction with SATRP, have invested R9 million in an initiative known as The Waste Tyre Management Plan. SATRP claims that almost 85 percent of tyre manufacturers are behind this plan.
As it stands right now, the Redisa plan has been gazetted and could go ahead as soon as public comments have been heard and necessary changes have been made. SATRP and the RMI have resubmitted their plans and are awaiting feedback from the minister. Consensus is that the matter has become a competition, and that this is not in the country’s best interests. The organisations involved are arguing among each other while the already-huge backlog of waste tyres continues to grow.
The final plan, once implemented, stands to colect but not necessarily profit about R600 million a year. According to Redisa, 80 percent of this would need to be put back into the broader recycling process, the remainder going to other operational activities.
So what now?
Waste tyre processors are a critical component of any tyre recycling plan, and external vendors are strongly relied on to come forward with tenders for contracts. However, different types of tyres require different methods of waste management, and there are also capacity variables for different locations to take into consideration.
Transportation costs are likely to be the biggest cost factor, and can be expected to rise with fuel price increases and the looming open road tolling system.
As it stands, the Redisa plan intends to recoup these costs by charging R2,30 for every kilogram of processed tyres received from subscribers and the levying of a waste tyre management fee. The latter has been built up around costs associated with transport, administration, research and development, training, depot management, marketing and social upliftment. The SATRP plan will make use of a similar fee.
The plan put forward by the RMI would see the implementation of a “green levy”, which would be established specifically for the purposes of the waste tyre management plan, and would obtain funds predominantly from producers and importers of tyres, and retreadable casings.
Like most recycling efforts, the first and foremost aim when recycling tyres is to reduce the amount of product needing to be recycled – which is addressed through consumer education.
Consumers need to become aware that the lifecycle of a tyre can be lengthened, and that this can save them money and help prevent irreparable damage to
the environment.
Maintaining the correct parameters for both vehicles and tyres will significantly extend the lifespan of tyres – tyre pressure maintenance, wheel alignment and balancing are simple yet effective methods. Another way to lengthen tyre life is through route planning and scheduling in order to reduce the distances travelled. This will also lead to lower fuel costs.
The next step once a tyre has reached the end of its useful life is retreading. Retreading saves up to 75 percent of the resources required to manufacture a new tyre, and contains the highest percentage of all post-consumer recycled materials.
While fuel and tyres are the highest fleet operational costs for fleet managers, they are now realising that, unlike fuel prices which they cannot change, tyres and tyre-related expenses can be managed.
The recycling of tyres is something that requires significant monetary input. Regardless of the way the rubber is recycled, it remains an expensive process, and with the quality of recycled rubber being equal to or less that of virgin rubber, the tyre recycling business isn’t always seen as appealing.
Large shredders are used to shred tyres into strips that are then processed into chips which can be used for various applications – from floor mats, truck and van liners, and sports turf to drainage pipes, non-slip paints and the soles of shoes.
There is also pyrolysis – a process where tyres are heated in an oxygen-free environment and, through a vaporisation process, an oily liquid that can be used as a fuel is obtained.
The public’s perception of incineration makes energy recovery hard to promote, however. The temperature that tyres burn at in open air isn’t high enough to completely incinerate all the toxic chemicals – they are released into the air and subsequently find their way into the soil and water supplies.
However, on a weight basis, tyres offer a 20 percent higher energy content than coal when used as a combustion fuel – and while the sulphur content of rubber is equal to that of coal, it releases fewer contaminants per unit of energy produced. This process of energy recovery is but one way old tyres could be put to good use.
Whatever happens from here, all associated parties will have to burn some serious rubber to make this work … (pun completely intended).
Published by
Focus on Transport
focusmagsa
