Talking power, too
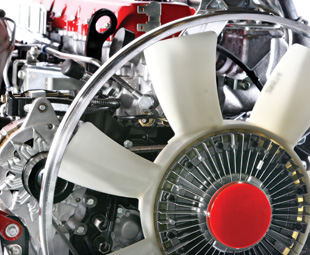
In his previous article, JAKE VENTER showed that, when rotation takes place in an engine, the work done is equal to the torque multiplied by the angle turned through. This month, he continues to look at the relationship between power and torque.
In February’s edition of FOCUS, we explored why, in the case of an engine, we can write: work done = TA where T is torque in Nm and A is the angle turned through, which is normally a number of revolutions. Let’s take this a little further.
Engineers don’t like to measure angles in degrees because it makes the mathematics cumbersome. Instead, they work in radians where one revolution or 360° is defined to be equal to 2π radians (π has its usual value as the ratio between the circumference and diameter of a circle). The work done during one revolution therefore becomes: work done = 2πT.
In our last article, we also showed that the work done divided by the time taken is equal to the power developed. For an engine, the time is introduced in the form of revs per minute (N), but the basic definition requires time to be in seconds, so that N r/min becomes N/60 revs per second. We can now write: power in watts = 2πTN/60. If we divide each side of our equation by a further 1 000, we can change our formula to give us power in kilowatts (kW): power in kW = 2πTN/60 000.
Although this formula explains the relationship between power and torque, the ratio 2π/60 000 is only a number to get the units right. In other words, it’s there just to make sure that if we feed in Nm and r/min we will get kilowatts out. More simply put, we can say that the kilowatts developed are proportional to the torque times the revs.
Now we can answer the question that so many people have asked: “What is more important when looking at a vehicle’s specs, kilowatts or torque?” The answer is that – since the definition of kilowatt involves time as a component in the form of revs per minute – any aspect of performance that can be measured with a stopwatch, such as acceleration times or speed, depends on kilowatts.
In the same way, any aspect of performance that does not need a stopwatch to be measured – such as an engine’s pulling power up a hill – depends on torque, because the basic definition of torque does not involve time.
Another way of looking at this is to realise what happens when a vehicle cruises at a particular speed. Because the definition of speed involves time, the kilowatt is the most important measure. For example, a small car needs about 12 kW to maintain 100 km/h, which can be maintained in any of the car’s top three gears. In each gear the engine speed and torque developed will be different, but when these values are incorporated into the formula for power the kilowatt value will be the same in all three gears. The drop in engine revs as each higher gear is selected will be matched exactly by the increase in torque put out by the engine.
This is a surprising result, although it’s true that an engine carries more load in higher than in lower gears. Which explains why lugging (employing large throttle openings in higher gears at a low engine speed) is bad for an engine. It also explains why a worn clutch first starts to slip in top gear while you can still travel without slip in lower gears. This means that the gearbox is a torque multiplier. While it does not change power – except for a small loss due to friction inside the gearbox – the torque at the gearbox output shaft is equal to input torque multiplied by gear ratio.
The torque at a vehicle’s driven wheels is thus equal to the torque developed at the engine flywheel multiplied by the gear ratio employed as well as the final drive ratio. For example, an engine developing 500 Nm at the flywheel will show a reading of 2 000 Nm at the output shaft of a gearbox employing a 4:1 first gear ratio and 10 000 Nm at the driven wheels if the differential ratio is 5:1. The diff splits this torque in half so each wheel will get 5 000 Nm. This is the sort of torque you need to pull away from standstill in a heavy truck.
Published by
Focus on Transport
focusmagsa
