Timber!
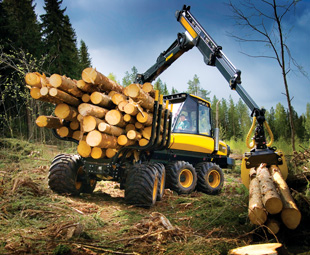
Highly specialised and rugged equipment is used in forestry operations. CLAIRE RENCKEN takes a look at how Matriarch Equipment came into being and what it has to offer this sector.
In 2009, the Bell brothers – Justin and Ashley – identified a gap in the marketplace for high-quality, locally produced handling equipment for the timber industry, and so Matriarch Equipment was born. The brothers set out with a vision of developing loading and extraction machinery, but decided that timber grapples were a good product on which to “cut their teeth” in the manufacturing game.
“We started from scratch and needed to establish certain systems and processes within the business in order to lay the foundation for the development, manufacture and support of our products going forward,” explains Ashley. That turned out to be a good move … In a short time, their grapples have become a common sight at timber harvesting sites and loading depots around the country.
The initial plan was to develop only two sizes – a 0,35 m² version and 0,41 m² version – as these are commonly used in the timber industry on tri-wheel loggers and trailer- or truck-mounted cranes.
The MT360 (0,35 m²) and MT420 (0,41 m²) grapples were accepted so well by the market that, soon after their launch in February 2010, requests for larger capacity grapples came pouring in.
“Grapples are high-wearing components within a timber harvesting operation and should be viewed as such,” says Justin. “There comes a time when repairing an old grapple is not financially viable in the short to medium term.”
Matriarch Equipment now produces nine different models of timber grapples, from the MT360 (0,35 m²) to the much larger MT1800 (1,8 m²). The company supplies grapples mostly to the southern African market, but has, in the past, also supplied to markets abroad, such as Malaysia, Indonesia and South America.
Justin explains: “Matriarch grapples feature a high-wear-resistant plate on the grapple jaws and a top rotator mount plate, as well as gussets on the grapple carrier. In addition, a twin-link arm and central cylinder more evenly distributes forces through the grapple carrier. This superior geometry helps to reduce the twisting force to prevent fatigue failure of pivot bosses and uneven wear on pins and bushes.”
All pivoting components are secured by a 50 mm pin with taper locks. Taper caps expand over the tapered ends of the pin and lock into the bore of the plate. “Provided these pins remain torqued up, as per our recommendation in our installation/maintenance manual, minimal wear will occur,” he adds. While greasing is recommended at every shift, the grapples also have perforated bushes to help to retain grease in the pivot joints where it is required.
In 2012, the company outgrew its factory in Richards Bay and moved into a new facility on a farm near Empangeni. Then, a year ago, Bell Equipment partnered with Matriarch Equipment and the latter’s grapples are now produced in Bell Equipment’s manufacturing facility in Richards Bay. Matriarch grapples are now being offered by Bell as an option in its range of loggers.
Bell Equipment product marketing manager: sugar, forestry and agriculture, Tim Beningfield, says: “Matriarch’s compatible design philosophy combined with Bell Equipment’s manufacturing capability is a winning formula. While our customers benefit from a modernised design with important features, we are able to add a superior product to our offering that has been designed with the customer’s input provided directly to the design engineers.”
At the same time, Matriarch’s slew loaders were also added to Bell Equipment’s agricultural offering. Back in 2011, Matriarch Equipment built its first two prototype slew loaders, one of which was converted for timber. It was tested for loading timber at railway sidings and was also used to do in-field loading of timber, proving the machine’s versatility.
The original idea was to design the slew loaders from scratch, but, in the end, the Matriarch team decided to use an excavator upper structure, coupled with a four-wheel-drive undercarriage and 0,5 m2 timber grab designed and built by Matriarch, which was optimised for loading operations.
“The big advantage of our slew loaders is that they are highly mobile, and can be used at a depot or in the field, and they don’t need a low-bed trailer to be moved from one site to another,” explains Justin. The maximum travel speed of the loader is 20 km/h.
In addition to the development and manufacture of products, Matriarch Equipment is also an importer and distributor of Indexator Rotators from Sweden. Various heavy-duty rotator models are offered by the company, which also holds a comprehensive stock of Indexator spare parts to ensure adequate support of the product in the field.
Research and development (R&D) play a major role in day-to-day operations at Matriarch Equipment. “Without R&D we’re at risk of falling behind the curve, so a great deal of emphasis is placed on this area of the business,” says Justin. The Bell brothers view innovation as the key to the survival of the business in the long term.
Published by
Focus on Transport
focusmagsa
